Increasing Cleaning Power and Water Savings for a Cosmetic and Personal Care Production Line
Insight
With increasing customer interest in sustainable products, reducing environmental impact is essential to consumer brands. Ecolab partnered with a large, multinational cosmetic and personal care company to identify opportunities to maximize productivity and reduce total operational costs while adopting sustainable operations in line with their corporate sustainability goals.
Innovation
The customer was looking for ways to improve operational efficiencies and wanted to reduce the time and water it took to clean the vessels used to produce their cosmetics. Makeup and personal care products are regulated, and the vessels used to produce them must be cleaned and sanitized according to a strict standard. The customer needed a global cleaning solution that would maximize each facility’s production capacity while helping ensure a high standard of quality.
The Ecolab team partnered with them to identify opportunities to target tough-to-clean product residues like titanium oxide, zinc oxide and silicon in their product lines while also reducing production stoppages, manual handling risks to employees from supplemental manual cleaning and the amount of water used to clean each vessel. Ecolab worked with one of the customer’s facilities to optimize their existing cleaning programs with our Risil Mat™ technology, an innovative alkaline detergent ideal for removing stubborn personal care and cosmetics processing residues. Risil Mat™ provided the facility with a safe and reproducible solution that allowed them to get their vessels clean on the first time.
Impact
The Ecolab Risil Mat™ program helped significantly reduce the need for manual cleaning — helping the customer increase their production capacity, enable safer operations and work more sustainably. Thanks to Risil Mat’s™ compatibility with existing equipment, the program also reduced costs by eliminating the need for immediate new capital investments or expansion to meet their production targets. In addition, the plant reduced significant water, energy and greenhouse gas emissions across the production line, demonstrating their commitment to sustainability to their customers.
The plant reduced significant water, energy and greenhouse gas emissions across the production line, demonstrating their commitment to sustainability to their customers.
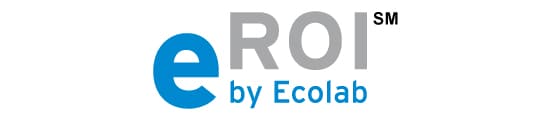
Annual Savings
WATER
48%
reduction in water use, equivalent to
96,000 gallons
ENERGY
31%
reduction in energy use, equivalent to
4,900 kWh
GREENHOUSE GASES
31%
reduction in carbon dioxide emissions
PRODUCTIVITY
50%
reduction in cleaning time and
9%
increase in capacity
HUMAN HEALTH
Increased employee safety and optimized physical cleaning procedures
Total Value Delivered
US$ 360
THOUSAND